Maintaining excellence at the NFCE
ADVANCED TECHNOLOGY FUELS | NUCLEAR FUEL CENTRE OF EXCELLENCE | UNIVERSITIES AND ACADEMIA | WORLD-CLASS FACILITIESThe Nuclear Fuel Centre of Excellence (NFCE) unifies top UK talent to resolve national clean energy security and establish a high-value nuclear economy. Rob Harrison, Research Fellow at the University of Manchester, explains how AFCP is strengthening the NFCE framework through skill retention, infrastructure investment and supply chain collaboration.
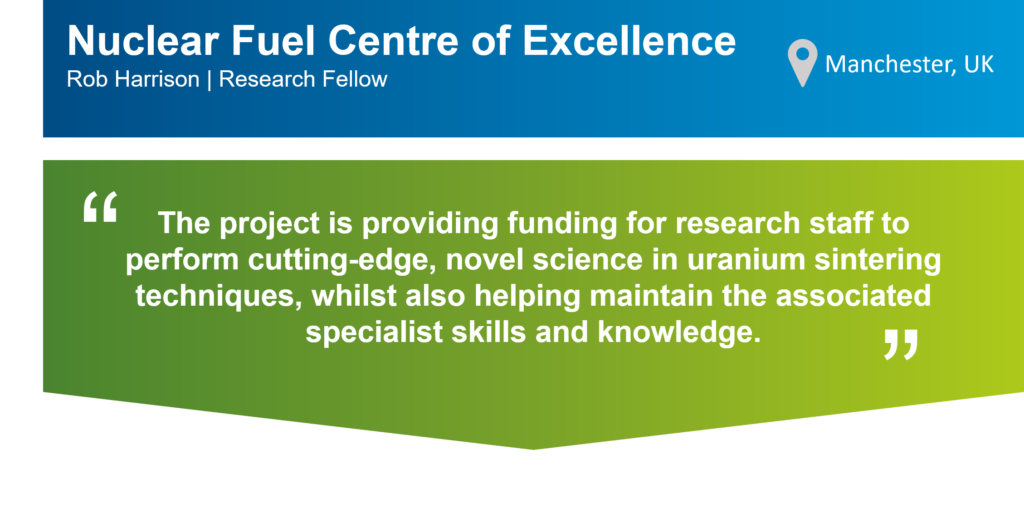
Challenge
Strategic investment to strengthen research reputation
The Nuclear Fuels Centre of Excellence (NFCE) at the University of Manchester leads cutting-edge research on new fuels and manufacturing methods. However, investment is required to ensure the UK maintains its strategic capability to carry out this research and that the facility is used to its fullest potential.
Solution
Connecting existing framework with new capability
This AFCP project will look at how advanced, electric field assisted sintering techniques can affect subsequent fuel material properties compared with conventional manufacturing routes. In conventional sintering, very high temperatures (>1700°C) and hour-long hold times are needed to manufacture nuclear fuel pellets. In electric field assisted sintering, an electric current is passed through the furnace and/or fuel pellet to enhance the sintering, which can dramatically reduce the temperatures and times needed to manufacture nuclear fuel pellets compared to conventional sintering.
NFCE already houses a uranium active spark plasma sintering furnace that AFCP is using in this study. In spark plasma sintering, electric current is used to create very high heating rates (up to 1000°C/min) and the furnace also applies a pressing force to the fuel pellet to reduce the sintering temperature to ~1300°C and time to minutes to produce the fuel pellet.
Additionally, as part of this AFCP project, the NFCE will install and commission a uranium active flash sintering furnace in partnership with Lucideon Ltd and the National Nuclear Laboratory (NNL). This new flash sintering furnace will pass electric current directly through the fuel pellet and can potentially reduce the sintering temperatures and times further, to ~600°C and seconds, respectively.
Impact
Retaining key skills to manufacture the fuels of the future
This partnership of AFCP projects will demonstrate the feasibility of flash sintering to manufacture nuclear fuel pellets using uranic material at the NFCE. The bespoke furnace designed by Lucideon Ltd will be the first bespoke flash sintering furnace designed specifically for use on nuclear fuel materials – giving unparalleled capability and control over previous systems adapted for flash sintering. Additionally, by testing on real uranium containing fuel pellets at the NFCE, we can optimise and demonstrate the process on real-life nuclear fuel materials for NNL to then evaluate the system for production of uranium and plutonium-bearing fuel materials .
The new flash sintering furnace will help NFCE maintain its state-of-the-art capability in uranium fuel manufacture. It will also further develop the techniques feasibility as a route to manufacture nuclear fuel pellets as well as training and developing academic researchers and industrial partners in its use on uranium active material. This knowledge and experience may then be transferred into NNL and the nuclear industry where higher activity materials can be handled to support trials and development of flash sintering on mixed uranium-plutonium fuels, which may be used in future fast neutron reactors – helping to develop a road-map in the re-use and reduction of the UK’s stockpile of plutonium.
The project is providing funding for research staff to perform cutting-edge, novel science in uranium sintering techniques, whilst also helping maintain the associated specialist skills and knowledge. Retaining skills in active uranium handling and operation of the equipment in the NFCE is imperative to it maintaining its capability to conduct cutting-edge research into the manufacture, characterisation and testing of uranium fuels. Furthermore, it acts a source of highly trained personnel for the nuclear industry, supplying both technically qualified staff in alpha radionuclide handling as well as other areas such as nuclear policy and regulation.
AFCP is part of the Department for Business, Energy and Industrial Strategy (BEIS) £505m Energy Innovation Programme.