Creative collaborations from afar
ENGAGEMENT | NNL | PYRO-PROCESSING | UNIVERSITIES AND ACADEMIACross-country research raises many challenges, all of which have been amplified through COVID-19. However, through ongoing engagement and sharing of strengths, AFCP’s pyro-processing teams at NNL, the University of Manchester and University of Edinburgh found a silver lining. Colin Clarke, Senior Research Technologist at NNL, comments.
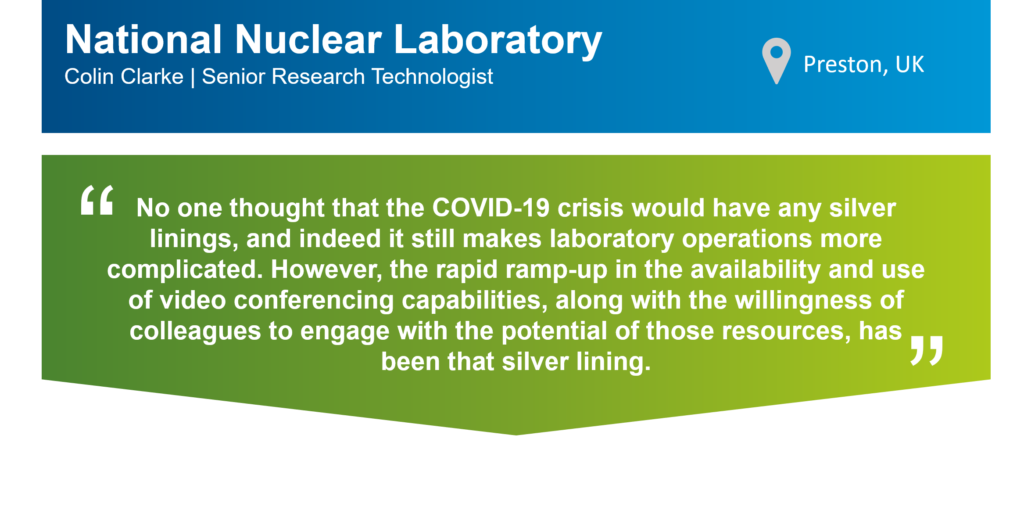
Challenge
Facilitating research across facilities
AFCP’s pyrochemical processing, or pyro-processing, workstream aims to give new life to used fuels while minimising the environmental impact of doing so. Pyro-processing offers several benefits for future fuel cycles, including superior radiation tolerance, intrinsic proliferation resistance and increased versatility.
While reliable process monitoring and control technologies are important for operating any plant-scale process, they are essential for commercial nuclear fuel treatment facilities. However, the development of an instrumentation architecture for pyro-processing raises a significant technical challenge. As pyro-processing matures and becomes part of the UK’s clean energy mix, we will require instruments to function accurately, consistently and reliably under the particularly harsh operating conditions – high temperature, high radiation and corrosive nature – of molten salts.
With the National Nuclear Laboratory, the University of Edinburgh and the University of Manchester, our pyro-processing project is applying a molten salt electrolyte for reprocessing used nuclear fuel. AFCP is developing two techniques with potential to provide non-destructive (or hardly destructive) methods of monitoring reactants and contaminants in molten salt solutions. The University of Edinburgh is developing micro-electrodes, or miniaturised chemical sensors, while the University of Manchester is developing laser-induced breakdown spectroscopy (LIBS).
Not only does this work present a geographic challenge – with the two measurement techniques centred at different academic institutions – but it also raises significant technical considerations. Developing these widely different, although hopefully complimentary techniques, is a difficult task. Both technologies – as well as the overarching pyro-process we are monitoring – are relatively low Technology Readiness Level (TRL), meaning that they require substantial development to reach a maturity at which they could be deployed for manufacture.
Additionally, the process streams that both teams are measuring are highly reactive. This makes them difficult to transport, which multiplies the complexities of the benchmarking task. To benchmark these two methods, it is vital that the two teams understand the systems under examination. They must work closely together to replicate samples and share knowledge about those sample solutions, including how to handle and prepare these solutions for measurement at high temperatures (350°C).
Solution
Bridging expertise through digital engagement
Our geographic challenge only expanded due to the coronavirus pandemic. With teams unable to meet in-person and with transport of samples hindered, we had to reconsider how to keep our project moving.
No one thought that the COVID-19 crisis would have any silver linings, and indeed it still makes laboratory operations more complicated. However, the rapid ramp-up in the availability and use of video conferencing capabilities, along with the willingness of colleagues to engage with the potential of those resources, has been that silver lining.
AFCP’s academic partners have eagerly adapted NNL’s experience in the handling and transport of hazardous and reactive materials. NNL has leveraged its skillset in reactive materials and experience in collaborative research to encourage and enthuse both Edinburgh and Manchester. With bi-weekly project meetings involving the whole project team from NNL and both universities, electronic communication platforms have generated productive, three-way discussions to help our teams reach new solutions together.
Impact
Playing to strengths for streamlined results
The use of video conferencing has facilitated open, technical conversations on the practical problems our teams have experienced. With a slew of suggested solutions now tabled, our project has been able to proceed in ways we wouldn’t have imagined given COVID-19 limitations.
Through these collaborations, we have been able to find specimen salt formulations that allow both techniques to demonstrate their capabilities. At the same time, this has allowed the team to benchmark the two techniques. This benchmarking enables us to directly compare the data derived from the two techniques, despite being from two different locations. This allows for greater understanding of the two analytical techniques and the molten salt solutions.
In addition, we have rapidly found solutions on how to exchange samples. NNL has played a key role through applying its experience of transporting sensitive material. This has allowed our academic partners to focus on their own strengths and share these with one another – maximising the potential of everyone involved in the project.
This work lays the foundation for our project’s success, ultimately supporting the future deployment of pyro-processing as part of the UK’s clean energy landscape. Securing the basic ability to take a measurement of typical lithium chloride solutions has been a great achievement as we work toward this goal. We have developed both the measurement systems and data analysis techniques to allow us to extract information from those systems. In doing so, we can transition to a point where we can design robust hardware that allows us to deploy those systems in a future pyro-processing manufacturing environment.
“The development of microelectrode detection at Edinburgh and LIBS detection at Manchester, each seen through the lens of the sensing and monitoring challenges of pyrochemical reprocessing, has been accelerated by the collaborative partnership, shared experiences and group discussions enabled by AFCP.”
Prof. Andy Mount, the University of Edinburgh
“Exploring two complementary techniques, LIBS (Manchester) and electrochemical microsensors (Edinburgh), for difficult in situ molten salt chemical characterisation has been facilitated and brought together under AFCP. This has enabled much wider interaction and collaboration, better developing the necessary expertise than would have been possible otherwise.”
Prof. Philip Martin, University of Manchester
AFCP is part of the Department for Business, Energy and Industrial Strategy (BEIS) £505m Energy Innovation Programme.