How to take the lead in reaching Net Zero
Lead-cooled fast reactors have great promise for the UK’s sustainability and clean energy commitments, but their deployment has so far been hindered by reactor chemistry and materials challenges. Working to accelerate the future of these novel nuclear reactors, NNL newcomer and AFCP researcher Akeel Ahmed gives the lead lowdown.

Since joining the National Nuclear Laboratory (NNL) in January 2021, I’ve been quick to pick up fast reactor knowledge on the Advanced Fuel Cycle Programme (AFCP).
Earlier this year, the Italian National Agency for New Technologies, Energy and Sustainable Economic Development (ENEA) delivered online seminars about lead technology for fast reactors. ENEA and NNL are project partners of Westinghouse with funding from Phase 2 of the Advanced Modular Reactor (AMR) competition supporting the development, demonstration and ultimately deployment of the first lead-cooled fast reactor in the UK. This reactor could become an integral part of the UK’s low-carbon and sustainable energy system.
Alongside other NNL colleagues and partners of Westinghouse, I attended the course as an introduction to some of the work I’ll be supporting under AFCP. The seminars were not only an immersion into lead-cooled fast reactors and existing international test facilities, but also demonstrated the value of international collaboration and knowledge exchange for achieving Net Zero.
From chemistry to AFCP
As an Operations and Technical Support Scientist at NNL, a key part of my work is within AFCP’s Fast Reactor Fuels project. Here, I’m supporting the development and testing of new fuel pellets for potential use in advanced reactors.
I’m also involved in the installation and ultimately operation of the flexible mini fuel line at NNL. One of AFCP’s ten new UK capabilities, the flexible mini fuel line will become a key piece of UK infrastructure for cutting-edge fuels research. Additionally, I’m working on the NNL side on the setup of a domestic lead testing facility to investigate materials corrosion in collaboration with Bangor University. This facility, in conjunction with others being developed as part of the Westinghouse’s AMR programme, will fill a current research gap in the UK, enabling researchers to investigate the interactions between lead, potential fuel and structural materials.
Prior to joining NNL, I completed an integrated master’s in chemistry and a PhD studying the anti-corrosion mechanism of graphene-based composite coatings, both at the University of Manchester. Due to my background in corrosion – and my involvement with AFCP’s lead corrosion testing work with Bangor University – I attended the training course to develop a greater understanding of the opportunities and challenges that these technologies present.
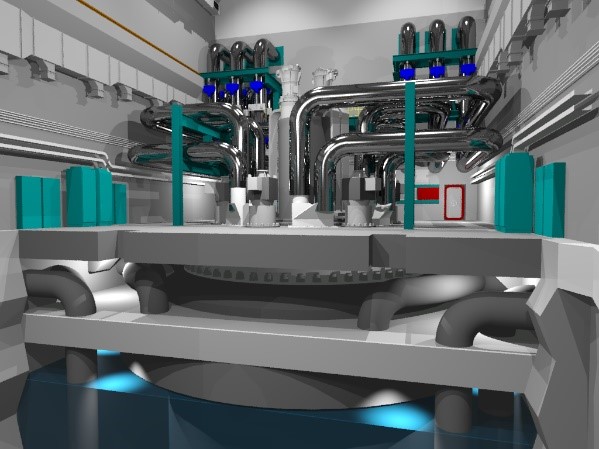
A review of fast reactors
Given the significant global demand for low-carbon energy systems, fast reactors are a relatively mature and promising technology that are currently receiving renewed interest in both the UK and globally. With power-dense cores and high-outlet temperatures, fast reactors can support process heat while operating with a sustainable fuel cycle that efficiently uses resources. They can therefore generate clean energy while significantly reducing the environmental impact of doing so.
There are currently three main types of fast reactors: liquid metal-cooled, gas-cooled and molten salt-fuelled fast reactors. The use of advanced and non-water-based coolants means that they enable greater plant efficiency and simplification. This means that fast reactors can support deeper decarbonisation.
Several nations have historically developed and operated sodium fast reactors, with a small subset of countries – including Russia, India, China, Japan – still operating them today to different extents. In the UK, we operated fast reactors using sodium or sodium-potassium alloys as a coolant. However, the UK ended its extensive fast reactor experience in the mid-1990s. We’re now experiencing a skills and facilities gap in the intervening 25 years. As we revisit fast reactors for Net Zero, we’re considering how to revive sodium capability as well as explore novel lead options to address gaps across both technologies.
Although lead fast reactors have not yet operated commercially, they have recently attracted significant interest due to their intrinsic safety and economic benefits. Notably, in June 2021, Rosatom poured the first concrete for the 300 MWe BREST-OD-300 lead fast reactor plant at the Siberian Chemical Combine site in Seversk, Russia. The plant is anticipated to be completed by 2026 as part of a pilot demonstration power facility that also includes on-site fuel manufacturing and reprocessing.
In addition, several other countries, including the UK through Westinghouse, are investigating lead fast reactors as part of their future clean energy systems. As such, it is necessary for the UK to utilise international knowledge – such as that provided in seminars such as the one I attended – to bring new life to our previously used fuel.
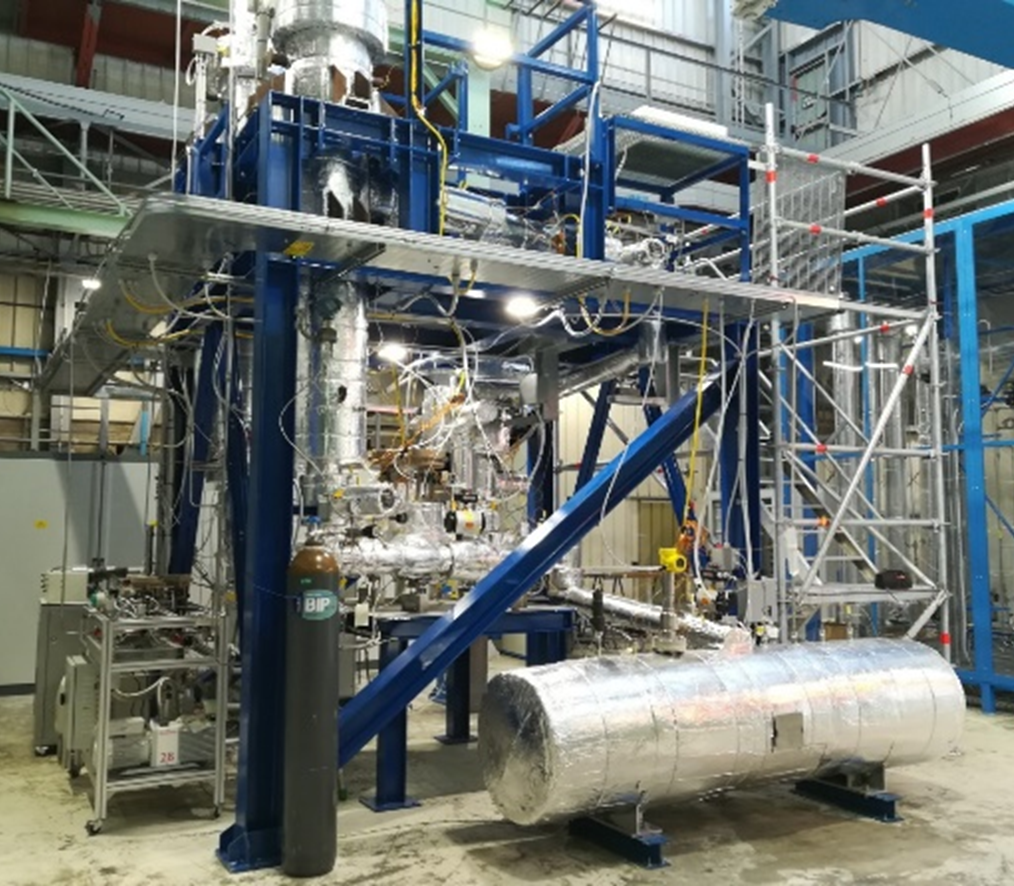
Leading a sustainable future
Why lead-cooled fast reactors? To understand this new interest, it’s important to first understand the wider fuel cycle.
To create nuclear energy, reactors consume fuel, most often uranium, which generates unstable and long-lived radioactive minor actinides. These include the elements in reactors other than uranium and plutonium, such as americium and neptunium. In an open fuel cycle – in which materials are used once and then disposed – these minor actinides are sent for long-term storage.
AFCP is supporting advanced, sustainable – or closed – fuel cycles. This allows us to keep materials within the nuclear fuel cycle as long as possible. Rather than going straight to storage, there has been a drive to consume plutonium and the other minor actinides to minimise waste, increase sustainability and realise the full potential of these elements.
Currently, there is a large stockpile of used fuels in the UK. These used fuel materials have been previously used in nuclear reactors and contain long-lived radioactive minor actinides. Through developing efficient, safe methods of reprocessing and separating these materials, AFCP is creating new ways to consume plutonium and the other minor actinides in specially designed reactors.
Fast reactors have the capability to efficiently burn minor actinides and reuse the long-lived isotopes that were previously sent for storage as fuel. Idaho National Laboratory previously found that in thermal reactors, the percentage efficiency of uranium is below 1%. In contrast, fast reactors have the potential to give efficiencies of ~10% for an open cycle, with significantly higher efficiencies when including reprocessing.
We can therefore get more energy while using less.
Navigating dense challenges
If lead is such a promising solution, why haven’t these reactors been deployed yet? Although harnessing lots of potential, lead fast reactors come with some notable challenges due to some of the unique properties of lead itself.
Most people associate lead with its high density. In a reactor, this can cause erosion problems due to the flow of the liquid coolant. Lead also has a high affinity with other materials, meaning that it can initiate corrosion of several conventional steels used in the reactor and as fuel cladding.
However, this corrosion challenge is not absolute in nature since it depends on temperature. This demonstrated by the successful long-term operation of more than 70 out-of-pile testing facilities internationally, which have operated with lead and lead-bismuth eutectic as coolants. These facilities have run at temperatures generally below 500°C – temperatures well below that at which corrosion challenges become more difficult. But operating above 500°C has a favourable effect on plant economics, hence the growing interest in material development and testing at these higher temperatures.
Overall, both corrosion and erosion challenges can cause mechanical damage to the reactor, simultaneously increasing impurities in the liquid lead. This latter phenomenon can potentially result in the plugging of narrow coolant passages if coolant chemistry control is not properly managed. Finally, lead is both optically and opaque, meaning it’s not possible to see inside the reactor once the coolant has been added.
The challenges associated with using liquid lead as a coolant have delayed lead fast reactor deployment. But by using proper design, materials and precautions, we can address these challenges. For example, we can mitigate lead’s tendency to initiate corrosion and erosion by controlling the oxygen levels in the system and using advanced materials and coatings with harder, more erosion- and corrosion-resistant materials. Additionally, filtering devices that remove solid contaminants (such as oxides) can be used jointly with coolant chemistry control measures to overcome the challenge of contamination in liquid lead coolant. Furthermore, ultrasonic imaging can be utilised to visualise and monitor the internal components of the reactor, as previously established for sodium fast reactors.
This ENEA seminar addressed these solutions and more.
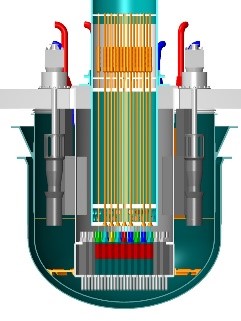
Learning from lead leaders
As part of the Advanced Modular Reactor competition Phase 2, ENEA hosted seminars on lead systems for organisations supporting Westinghouse on the programme, including NNL. The training course provided an overview to the development of the Westinghouse lead fast reactor as one type of a new generation of advanced modular reactors.
The seminars explored the challenges associated with using lead as a coolant and reviewed the current work in the field. This provided up-to-date knowledge and an introduction to the plans being put into place to support the development of the Westinghouse lead fast reactor.
With various experts from ENEA leading the training course, I was able learn about the work on lead reactors from a broader perspective. Attending the seminars provided me with an important background in various aspects of the field, such as lead corrosion, erosion and handling, coating chemistry and coolant chemistry. This learning experience has not only built on my PhD background, but has also enhanced my knowledge in key areas of lead-cooled reactors.
Given the UK’s present skills gap in this technology, these seminars provided an excellent overview of what lead fast reactors are and how to handle lead. Through AFCP, we’ll be applying these concepts in the development of the lead corrosion testing facility in collaboration with Bangor University and Westinghouse.
Fast tracking our way to Net Zero
The use of fast reactors is vital in developing closed fuel cycles to minimise the disposal of radioactive waste. Hence, the development of a lead fast reactor in the UK can be a steppingstone on the path to a more sustainable future.
The training course provided insights into the current state of lead fast reactors, as well as the outstanding R&D challenges and ongoing international activities to address these. This has allowed me to get an understanding of the potential work and issues that we may need to address when using the new lead testing facility at NNL. From a personal perspective, the seminars were very interesting for me, particularly the topics on corrosion and coatings, as they enabled me to relate back to my PhD and understand the application in an alternate field.
Opportunities like this are invaluable to the global clean energy community as we work toward more sustainable means of supplying low-carbon energy. It’s important that we think about not only the materials used (or reused, in the case of fast reactors) in energy generation, but also the people and skills supporting these systems. Through international engagement and knowledge sharing, we can ensure that these clean energy technologies can continue to evolve and succeed through generations to come.
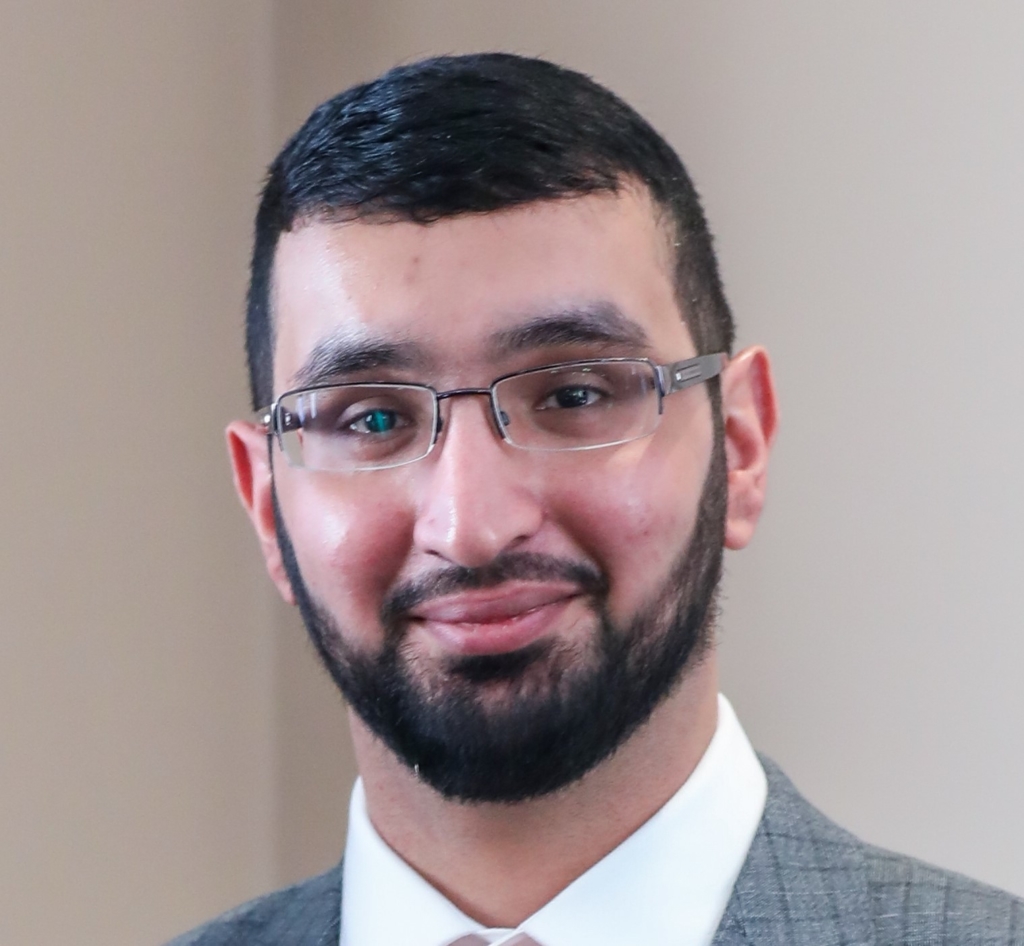
AFCP is part of the Department for Business, Energy and Industrial Strategy (BEIS) £505m Energy Innovation Programme.